What is Directed Energy Deposition (DED) 3D Printing?
Directed Energy Deposition (DED) is a metal additive manufacturing process where an energy source – usually an Electron Beam, Laser or Arc (PAW, GTAW, TIG) – is directed toward a plate or other substrate material where it impinges with wire or powder feedstock material and melts, leaving deposited material on the substrate.
The directed material flow and energy source generally move together, creating layer upon layer of metal with finite width and thickness.
In general, customers choose DED over other metal 3D printing methods because of its higher deposition rate and ability to additively manufacture larger parts (many of which wouldn’t fit within powder bed systems).
Below is a simple illustration of Sciaky’s Directed Energy Deposition method. With our DED technology (called Electron Beam Additive Manufacturing or EBAM®), we feed metallic wire directly into an electron beam to create metal preforms out of a molten substrate pool. Once the part reaches near-net shape, it undergoes finish heat treating, machining and inspection.
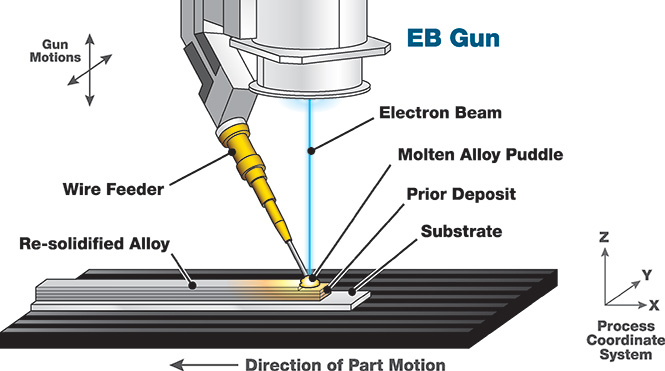
The power imparted to the substrate and material is controlled by the Electron Beam Gun’s current and accelerating voltage. Typical power values of our DED machines range between 5 and 20 kW, varying with material, deposition rate, and geometry. EBAM runs continuously for hours at a time, necessitating adaptive closed-loop control, which monitors the molten pool and dynamically adjusts the energy level. Currently, CAD modeling software is used to create the machine path, akin to 5-axis tool path planning used for CNC milling machines. Allowing for the purest metal applications, EBAM operates in a vacuum environment in the range of 1.3 x 10-2 to 1.3 x 10-3 Pa [1.0 x 10-4 to 1.0 x 10-5 Torr].
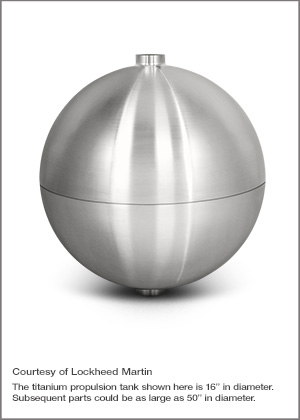
EBAM’s layer-by-layer deposition of feedstock material (Ti-6Al-4V or any reactive and refractory alloy) ultimately produces near-net-shape structures and parts up to 80% faster than traditional manufacturing methods.
As an example, the ability to rapidly procure components for the aerospace industry is severely limited by prohibitive (and worsening) lead-times for raw materials, tooling (casting molds, forging dies, etc.), design, and manufacturing time for components. EBAM preforms are created closer to the final geometry of many parts, which reduces the volume of raw material needed as well as the subsequent machining steps. This mitigates the need for hard tooling and improves the flexibility of the design process.
Other DED Methods
Laser Directed Energy Deposition Machines
When a Laser is the “Energy” piece of the DED equation, users can expect Laser DED Systems to achieve good feature resolution for smaller parts. They are generally simpler to operate than EB DED, use a relatively low heat input when using powder, and do not require a vacuum environment for the energy source. In theory, Laser DED could allow for inert cooling gas, improving cooling rates and creating finer microstructures.
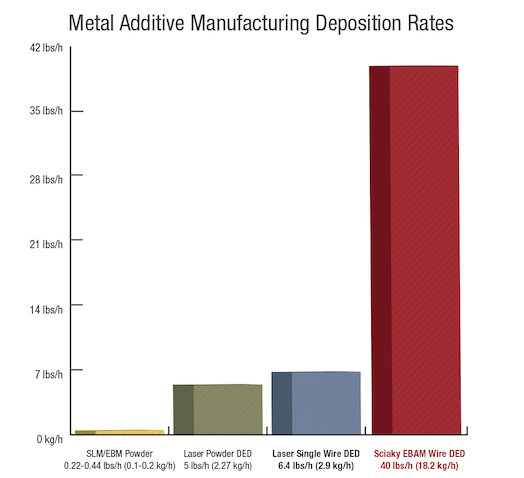
Some of the drawbacks of laser DED include material reflectivity issues, reliance on inert gas for shielding, energy source manipulation and beam raster challenges. And Laser DED’s small spot size and low energy input is not well suited to high deposition rates or large-scale parts. In contrast to Sciaky’s average Gross Deposition Rate of 40 lbs. of material per hour, many laser DED machines only deposit 1 to 2 lbs.
Arc Directed Energy Deposition Machines
Similar to how Electron Beam Welding machinery enabled the discovery of Electron Beam DED, Arc DED was adapted from Arc Welding.
Arc DED refers to three different Arc Welding technologies – Plasma Arc Welding (PAW) DED, Gas Tungsten Arc Welding (GTAW) DED, and Metal Inert Gas (MIG) DED.
Despite some differences between these machine types, all Arc DED technologies share some common distinctions and downsides. They are typically the least expensive DED systems on the market, with the least complicated energy source. They capably create near-net preforms with steel alloys. High power is available, though the deposition rate still lags far behind Electron Beam DED.
On the other hand, pure inert gas like argon is required to routinely operate these machines – and these can be expensive and hazardous. You may need to shield a large volume with inert gas if high deposition rates and travel speeds are attempted. Also on the cost side – torch components need to be changed frequently. Arc DED systems provide minimal control of arc plume to precisely address energy density of the source.
Questions about Comparing EB, Laser and Arc DED?
Many of the ideal use cases for EB DED are listed on our Applications & Industries page.
We’re at your disposal and are happy answer your questions as objectively as possible. Just shoot us a note from our Contact Page.