What is Directed Energy Deposition (DED) 3D Printing?
Directed Energy Deposition (DED) is a metal additive manufacturing process where an energy source – usually an Electron Beam, Laser or Arc (PAW, GTAW, TIG) – is directed toward a plate or other substrate material where it impinges with wire or powder feedstock material and melts, leaving deposited material on the substrate.
The directed material flow and energy source generally move together, creating layer upon layer of metal with finite width and thickness.
In general, customers choose DED over other metal 3D printing methods because of its higher deposition rate and ability to additively manufacture larger parts (many of which wouldn’t fit within powder bed systems).
Below is a simple illustration of Sciaky’s Directed Energy Deposition method. With our DED technology (called Electron Beam Additive Manufacturing or EBAM®), we feed metallic wire directly into an electron beam to create metal preforms out of a molten substrate pool. Once the part reaches near-net shape, it undergoes finish heat treating, machining and inspection.
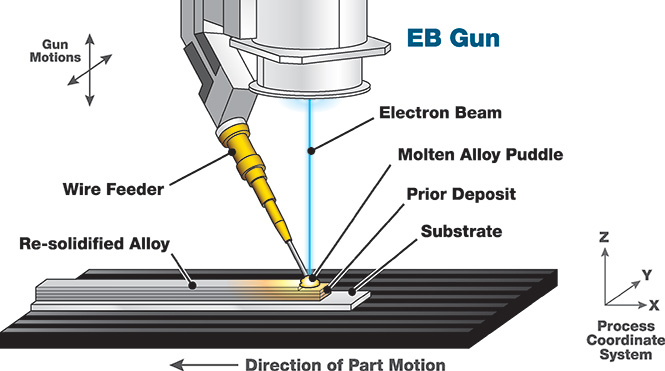
The power imparted to the substrate and material is controlled by the Electron Beam Gun’s current and accelerating voltage. Typical power values of our DED machines range between 5 and 20 kW, varying with material, deposition rate, and geometry. EBAM runs continuously for hours at a time, necessitating adaptive closed-loop control, which monitors the molten pool and dynamically adjusts the energy level. Currently, CAD modeling software is used to create the machine path, akin to 5-axis tool path planning used for CNC milling machines. Allowing for the purest metal applications, EBAM operates in a vacuum environment in the range of 1.3 x 10-2 to 1.3 x 10-3 Pa [1.0 x 10-4 to 1.0 x 10-5 Torr].
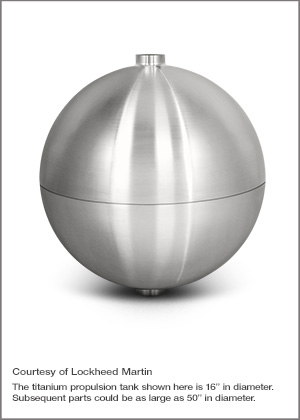
EBAM’s layer-by-layer deposition of feedstock material (Ti-6Al-4V or any reactive and refractory alloy) ultimately produces near-net-shape structures and parts up to 80% faster than traditional manufacturing methods.
As an example, the ability to rapidly procure components for the aerospace industry is severely limited by prohibitive (and worsening) lead-times for raw materials, tooling (casting molds, forging dies, etc.), design, and manufacturing time for components. EBAM preforms are created closer to the final geometry of many parts, which reduces the volume of raw material needed as well as the subsequent machining steps. This mitigates the need for hard tooling and improves the flexibility of the design process.
Other DED Methods
Laser Directed Energy Deposition Machines
When a Laser is the “Energy” piece of the DED equation, users can expect Laser DED Systems to achieve good feature resolution for smaller parts. They are generally simpler to operate than EB DED, use a relatively low heat input when using powder, and do not require a vacuum environment for the energy source. In theory, Laser DED could allow for inert cooling gas, improving cooling rates and creating finer microstructures.
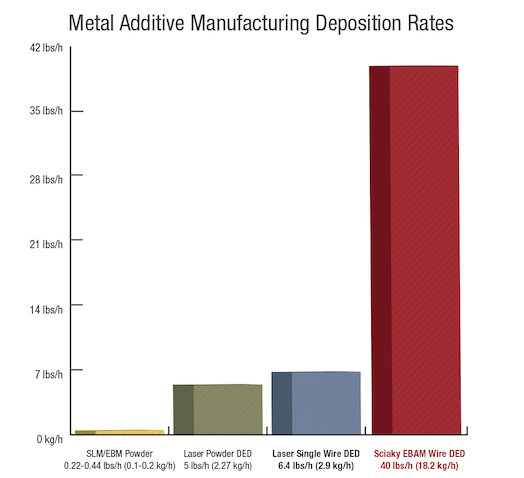
Some of the drawbacks of laser DED include material reflectivity issues, reliance on inert gas for shielding, energy source manipulation and beam raster challenges. And Laser DED’s small spot size and low energy input is not well suited to high deposition rates or large-scale parts. In contrast to Sciaky’s average Gross Deposition Rate of 40 lbs. of material per hour, many laser DED machines only deposit 1 to 2 lbs.
Arc Directed Energy Deposition Machines
Similar to how Electron Beam Welding machinery enabled the discovery of Electron Beam DED, Arc DED was adapted from Arc Welding.
Arc DED refers to three different Arc Welding technologies – Plasma Arc Welding (PAW) DED, Gas Tungsten Arc Welding (GTAW) DED, and Metal Inert Gas (MIG) DED.
Despite some differences between these machine types, all Arc DED technologies share some common distinctions and downsides. They are typically the least expensive DED systems on the market, with the least complicated energy source. They capably create near-net preforms with steel alloys. High power is available, though the deposition rate still lags far behind Electron Beam DED.
On the other hand, pure inert gas like argon is required to routinely operate these machines – and these can be expensive and hazardous. You may need to shield a large volume with inert gas if high deposition rates and travel speeds are attempted. Also on the cost side – torch components need to be changed frequently. Arc DED systems provide minimal control of arc plume to precisely address energy density of the source.
Questions about Comparing EB, Laser and Arc DED?
Many of the ideal use cases for EB DED are listed on our Applications & Industries page.
We’re at your disposal and are happy answer your questions as objectively as possible. Just shoot us a note from our Contact Page.
IRISS® Interlayer Realtime Imaging & Sensing System
Advanced closed-loop control system for optimizing the EBAM® Metal 3D-printing process
Motivation
Parts that are additively manufactured without a control system can have many quality issues. Since part quality for metal is affected by parameter settings in the deposition process, uncontrolled settings can lead to variability in layer geometry, mechanical properties, microstructure, and possibly chemistry. Traditionally, deposition settings and adjustment of parameters were analyzed by an operator and manually corrected, resulting in variable part quality. This limitation is possibly the single largest barrier to the adoption of Additive Manufacturing [AM].
Solution
Sciaky brings together both quality and control in one step with IRISS® – the Interlayer Real-time Imaging and Sensing System. IRISS is the only real-time adaptive control system in the market that can sense and digitally self-adjust metal deposition with precision and repeatability. Our closed-loop control is the primary enabler of Sciaky’s EBAM 3D printing process that through eliminating variations, results in improved quality and production throughput.
IRISS is a patented suite of sensors, software logic, and CNC controls that monitors key metal deposition parameters in order to make real-time adjustments to the deposition inputs. The data collected from the process is quantified and digested by our IRISS software algorithms. The outputs from the software will change deposition parameters such as EB power, wire feed rate, and CNC motion profiles. These adjustments are made dozens of times per second in order to guarantee that every ounce or gram of metal deposited experiences the same transition from wire, to liquid, to solid. This is to ensure consistent and reliable geometries, mechanical properties, microstructure construction and metal chemistry for medium to mega scale AM parts.
System Features & Benefits
- The IRISS real-time closed-loop control is integrated with Sciaky EBAM 3D-printing systems
- Digital parameter control and adjustments are made in response to real-time measured data, without process disruption
- Records every second of deposition, so the entire build can be reviewed, verifying consistency and keeping a record for later review
- Prevents surprises by dynamically adjusting parameters to maintain part integrity
- Better insures net shape fabrication and reduces post processing time and costs such as machining and inspection
Impact
Our innovative IRISS process control virtually eliminates inconsistencies from the first to the last layer. Because IRISS is self-adjusting, it maintains key process characteristics through the manufacturing cycle, which results in high-quality parts. The iterative nature of our control technology results in designs with greater complexity, performance and cost reductions, compared to passive, open-loop monitoring systems offered by others in the AM industry.
Benefits of Wire vs. Powder Metal 3D Printing
Comparing Sciaky's wirefeed 3D printing process, a.k.a. Electron Beam Additive Manufacturing, to powder-based feedstock 3D printing processes
While there has been no shortage of metal additive manufacturing (AM)/3D printing coverage in the media over the past few years, there has not been a great deal of attention placed on the different metal AM processes relative to supply material (known as feedstock). Most of the coverage has been built on powder-based feedstock systems with minimal comparison to melted wire as the supply material. In a nutshell, there are three primary feedstock process forms for metal AM: (1) Powder Bed, which includes Selective Laser Sintering (SLS), Selective Laser Melting (SLM), and Electron Beam Melting (EBM); (2) Powder Directed Energy Deposition, which covers Laser Engineering Net Shape (LENS), Laser Metal Deposition-powder (LMD-p), etc.; and (3) Wire Directed Energy Deposition, which includes commercially available equipment such as Laser Metal Deposition-wire (LMD-w) and Electron Beam Additive Manufacturing (EBAM®). We will take a look at a few of these processes and address the attributes that wire feedstock offers as a supply material for metal additive manufacturing.
Powder Bed AM Processes
Raw Material Used: Powder
Selective Laser Sintering (SLS) and Selective Laser Melting (SLM) are interchangeable terms that refer to a laser-based 3D printing process that works with powdered materials. The laser is traced along an X & Y plane across a powder bed of evenly spread material laid down by a leveler or roller on a build tray. As the laser interacts with the surface of the powdered material it sinters, or fuses, the particles together to form a solid. As each layer is completed, the powder bed drops incrementally and a roller smoothes the powder over the surface of the bed prior to the next pass of the laser for the subsequent layer to be formed and fused with the previous layer.
The build chamber is completely sealed as it is necessary to maintain an inert gas environment to shield the melting powder from oxygen contamination and to better maintain the temperature during the process specific to the melting point of the powdered material of choice. Once finished, the excess powder is removed, leaving the “printed” part. One of the key advantages of this process is that the powder bed serves as an in-process support structure for overhangs and undercuts, and, therefore, complex shapes with high geometrical accuracy of +/- 0.05 mm can be manufactured with this type of process which separates this AM technology from the others. [1], [8]
However, on the downside, porosity has been an historical issue with this process, and while there have been improvements towards fully dense parts, some applications still necessitate Hot Isostatic Pressing (HIP) or infiltration with another material to improve mechanical characteristics. Also, the cost of the inert gas required for the process, and the time to reach satisfactory processing conditions (oxygen content, gas purity, etc.), raise concerns.
Much like SLS/SLM, Electron Beam Melting (EBM) is a powder bed fusion technique. The key difference is the heat source, which, as the name suggests, is an electron beam, rather than a laser, which necessitates that the procedure is carried out under vacuum conditions.
The EBM process has been “labeled” slow and expensive, when compared to SLS/SLM. However, it has been particularly effective in the medical industry for creating implants. [1], [2] However, for all the powder bed processes, the deposition rate is very low and the fabricated component size is limited to the bed size, which restricts its application to relatively small components; typically less than 400 x 400 x 400 mm (15.7 x 15.7 x 15.7 inches) in length, width and height.
Directed Energy Deposition AM Processes
Raw Materials Used: Powder & Wire
Directed Energy Deposition (DED) utilizes focused energy (either an electron beam or laser beam) to fuse materials by melting as the material is being deposited. [3] Powder or wire feedstock can be utilized with this process.
Powder DED
Powder-fed systems, such as Laser Metal Deposition (LMD) and Laser Engineered Net Shaping (LENS), blow powder through a nozzle, which is melted by a laser beam on the surface of the part. Therefore, for the purposes of this study, we will also reference this method as a “blown powder” AM process. This process itself is highly precise and is based on an automated deposition of a layer of material with a thickness varying between 0.1 mm and a few millimeters. The metallurgical bonding of the cladding material with the base material and the absence of undercutting are some features of this process. The process is dissimilar to other welding techniques in that a low heat input penetrates the substrate. [4]
Wire DED
Laser-based wirefeed systems, such as Laser Metal Deposition-wire (LMD-w), feed wire through a nozzle that is melted by a laser, which incorporates inert gas shielding in either an open environment (gas surrounding the laser), or in a sealed gas enclosure or chamber. This process provides higher deposition rates as compared with powder bed and blown powder DED.
Sciaky's Electron Beam Additive Manufacturing (EBAM®) Process
The Electron Beam Additive Manufacturing (EBAM™) process, which is exclusive to Sciaky, Inc., utilizes wire feedstock and an electron beam heat source to produce a near-net shape part inside a vacuum chamber. Starting with a 3D model from a CAD program, which is converted to CNC code, Sciaky’s electron beam (EB) gun deposits metal, via the wire feedstock, layer by layer, until the part reaches near-net shape. Once the part reaches near-net shape, it undergoes finish heat treatment and machining. The process itself is scalable for components from millimeters to multiple meters in size, limited only by the size of the vacuum chamber.
A Quick Comparison: Wire vs. Powder
Raw Material Availability
In general, AM users will enjoy a wider selection and greater availability of wire products versus powder.
The Grainger Catalog lists 380 different welding wire products in stock at most of their hundreds of branches. This counts only the steel and nickel alloys that Grainger carries, and does not count any of the specialty alloys available from other outlets.
The following is a list of raw material available in wire feedstock:
- Titanium and Titanium Alloys
- Inconel 600, 625, 718
- Nickel and Copper Nickel Alloys
- Stainless Steels 300 Series
- Aluminum Alloys 1100, 2318, 2319, 3000 Series, 4043, 4047, 5183, 5356, 5554, 5556
- Alloy Steels
- Cobalt Alloys
- 4340 Steel
- Zircalloy
- Tantalum
- Tungsten
- Niobium
- Molybdenum
Cost
Based on supplier/Internet research, powder feedstock is more expensive than wire feedstock across the board.
For example, on average, AM-grade Titanium 6AI-4V powder is about 141% more expensive than the average cost of Titanium 6AI-4V wire – and Titanium wire generally has a faster turnaround time than Titanium powder (sometimes as much as 4 weeks). AM-grade Tantalum powder is 7% more expensive than the average cost of Tantalum wire. Dramatically, both AM-grade Inconel 625 powder and AM-grade Stainless Steel 316 powder are double the average cost of their wire counterparts. See the table below for more cost details; these costs were based on a survey of the U.S. commercial market in June 2015.
Material Feedstock | Titanium 6AI-4V | Tantalum | Inconel 625 | Stainless Steel 316 |
---|---|---|---|---|
Wire—0.035" Diameter |
$58/lb. |
$545.30/lb. |
$26.73/lb. |
$5.19/lb. |
Wire—0.045" Diameter |
$54/lb. | $545.30/lb. | $23.30/lb. | $4.63/lb. |
Wire—0.062" Diameter |
$50/lb. | $524.88/lb. | $22.17/lb. | $4.57/lb. |
Wire—0.093" Diameter |
$48/lb. | $502.30/lb. | $21.43/lb. | $4.81/lb. |
Wire—0.125" Diameter |
$45/lb. | $438.96/lb. | $21.02/lb. | $4.75/lb. |
Wire—0.156" Diameter |
$44/lb. | $438.96/lb. | N/A | $4.69/lb. |
Powder—AM Grade |
$120/lb. | $522/lb. | $48/lb. | $10/lb. |
Safety & Procurement Issues with Powder AM Approaches
In an article titled “What’s the Difference Between SLA and SLS?” in the April 2015 issue of Machine Design, Technology Editor Jeff Kerns states that “SLS powders raise safety concerns” because “breathing in fine particles, such as nickel, can be harmful.” Mr. Kerns then states “breathing apparatuses and ventilation should be considered depending on the type of powder.” The article also mentions that “SLS powders can be difficult to purchase.” [6] Furthermore, in an article titled “Navy going big on 3D printing next year” in the July 2015 issue of ECN, Lt. Ben Kohlman of the Chief of Naval Operations stated “There are significant safety concerns (with powder). The powder that’s used in the aluminum or titanium is highly flammable.” [5]
The Origins of Sciaky’s Wire-based EBAM® Process
Sciaky, Inc. began developing the wirefeed EB process back in the mid-1960s. The process was further refined to build jet engine knife edge seals in the 1990s, [10] and, in the early 2000s, the EBAM process was developed to help manufacturers save significant time and money on the production of large, high-value metal parts. In 2009, Sciaky formally launched the EBAM process (which was then marketed as Electron Beam Direct Manufacturing) as a service option. In 2011, Sciaky was selected by Lockheed Martin Aeronautics for the Department of Defense (DOD) Mentor-Protégé Program with the focus of this agreement being the additive manufacturing of titanium structural components for Lockheed Martin's F-35 aircraft program. In 2012, Sciaky entered a partnership with Penn State University, via DARPA (Defense Advanced Research Projects Agency) funding, to advance Direct Digital Manufacturing (DDM) technology with the goal of advancing and deploying DDM technology for highly engineered and critical metallic systems to the Department of Defense (DOD) and U.S. industry. In 2014, Sciaky began delivering turnkey EBAM systems to the commercial market. Lockheed Martin Space Systems was among the first customers to receive an EBAM system for developing and producing 3D printed titanium propellant tanks.
The Brains, Brawn and Exclusivity of EBAM®
The capability to achieve predictable and repeatable operations is important for wirefeed AM, and this is needed to increase the stability of the deposition process. [8] Sciaky’s patented IRISS® Closed-Loop Control technology is the brains behind EBAM. It provides consistent part geometry, mechanical properties, microstructure, metal chemistry and more, from the first part to the last part.
As for the brawn, EBAM gross deposition rates range from 7 to 40 lbs. (3.18 to 18.14 kg) of metal per hour, depending upon the selected material and part features, making it the fastest metal additive manufacturing process in the market. The reported maximum deposition rate of laser-based wirefeed is 48.0 g/min, which translates to 6.4 lbs. (2.9 kg) per hour. [8] Typical SLM and EBM metal powder AM approaches, on the other hand, produce 0.22 to 0.44 lbs. (0.1 to 0.2 kg) per hour. [7] In addition, powder-fed laser directed energy deposition methods (i.e. blown powder techniques) top out around 5 lbs. (2.27 kg) per hour.
On another note, EBAM can produce high quality, large-scale metal structures, larger than 19 feet (6 meters) in length, with very little material waste. With metal powder approaches, you typically need as much as 5 times the powder volume to build the part, with the majority of the material going unused, which must be reclaimed or discarded.
EBAM and other wirefeed processes are more environmentally-friendly due to the near 100% usage efficiency of the wirefeed to the melt pool; no feedstock reclamation is necessary.
Based on recent research carried out by faculty members at the Engineering and Information Sciences section of the Alliterative School of Mechanical, Materials, and Mechatronic Engineering at the University of Wollongong in New South Wales, Australia [9], the benefits of metal wire over powder-based laser sintering processes include the strength of wire (fabricated AM components) compared to the compacted powder of laser sintered metal parts. Because of the low deposition rates of the laser sintering process, the method isn’t ideal for creating larger objects, such as those that are likely to be used in aircraft engines, air frame structures or other large mechanical systems. Additionally, for industries that rely heavily on creating custom 3D printed parts on demand – especially those that need larger parts without the need for fine details – the wirefeed process is a no brainer.
Another critical advantage of Sciaky’s EBAM technology is that it can be equipped with multiple wirefeed nozzles utilized with a single EB gun. This option allows you to simultaneously feed, with independent program control, two or more different metal alloys into a single molten pool, which is ideal for creating “graded” or “super alloy” parts or ingots. In other words, you can change material compositions to create a new generation of alloys and functionally graded materials (FGM) for potential material performance advantages that are unavailable today. This build strategy can also allow different alloy mixtures in different locations on the part as determined by part function. This flexibility can also be used with different wire gauges to allow heavy deposition for gross features, while also allowing fine deposition features to be produced with thinner wire. These material process advantages are not available with the powder bed or powder injection (i.e. blown powder) AM processes.
Simply put, there is no other metal AM approach on the market that can do what EBAM does.
References/Resources
[1] 3dprintingindustry.com; 3D Printing Processes: The Free Beginner’s Guide
http://3dprintingindustry.com/3d-printing-basics-free-beginners-guide/processes/
[2] 3dprintingfromscratch.com; Types of 3D printers or 3D printing technologies overview
http://3dprintingfromscratch.com/common/types-of-3d-printers-or-3d-printing-technologies-overview/
[3] Wohlers Associates Industry Briefing, February 2013; Additive Manufacturing Process Categories
https://wohlersassociates.com/brief02-13.html
[4] Metal AM; Article titled “Metal Additive Manufacturing Processes”
http://www.metal-am.com/introduction_to_metal-additive_manufacturing/processes
[5] ECN: Article titled “Navy going big on 3D printing next year” by Bryant Jordan, Defense Tech
http://www.ecnmag.com/news/2015/07/navy-going-big-3d-printing-next-year?et_cid=4655278&et_rid=480122371&location=top
[6] Machine Design, April 2015 issue: What’s the Difference Between SLA and SLS? By Jeff Kerns, Technology Editor
http://machinedesign.com/3d-printing/what-s-difference-between-stereolithography-and-selective-laser-sintering
[7] Microstructural Evolution in Ti-6Al-4V Multi-Layer Builds Produced By Three Additive Manufacturing Processes; By S. Lathabai, M. Glenn, and D. R. Ritchie of CSIRO (June 17, 2014 AeroMat Conference presentation)
[8] Wire-feed additive manufacturing of metal components: technologies, developments and future interests; By D. Ding, Z. Pan, D. Cuiuri, and H. Li, 09 May 2015.
[9] 3ders.com; Wire-feed additive manufacturing might be the future of metal-based 3D printing; By Simon
http://www.3ders.org/articles/20150531-wire-feed-additive-manufacturing-might-be-the-future-of-metal-based-3d-printing.html
[10] AWS C7.1:2013, Recommended Practices for Electron Beam Welding and Allied Processes, Practical Examples 13.2 – Knife Edge Seal Using Electron Beam Additive Manufacturing Process
EBAM™ System with IRISSSM Closed-Loop Control Available April 2016
Model: EBAM™ 110x110x110
Price: Call for Details
Sciaky has an EBAM™ 110x110x110 available.
How does EBAM™ work? Starting with a 3D model from a CAD program, Sciaky’s electron beam (EB) gun deposits metal (via wire feedstock), layer by layer, until the part reaches near-net shape and is ready for finish machining. EBAM™ produces high quality, large-scale metal structures made of titanium, tantalum, and nickel-based alloys in a matter of days, with very little material waste. Sciaky’s patented IRISSSM closed-loop control technology provides consistent part geometry, mechanical properties, microstructure, and metal chemistry, from part 1 to 1,000. And with standard deposition rates ranging from 7 to 20 lbs. per hour, EBAM™ works faster than rival metal additive manufacturing processes.
EBAM™ 110x110x110 Specifications:
- Chamber Dimensions 110” (2794 mm) x 110” (2794 mm) x 110” (2794 mm)
- Work Envelope–70” (1778 mm) wide x 47” (1194 mm) deep x 63” (1600 mm) high
- Nominal Part Envelope–106” (2692 mm) wide x 47” (1194 mm) deep x 63” (1600 mm) high
- High Efficiency Pumping–Chamber Hard Vacuum (5 x 10-6 Torr)
- Power Level up to 42 kW–60 kV
- Internal Boom Mounted Gun with High Resolution Optics & Servo Gun Tilt Axis
- X, Y & Z Servo Axes with Multiple Part Positioner Options
- CNC Control–Joint Scanning and Digitizing System
- Wirefeed with Motorized Wire Nozzle (Dual Wirefeed System is Available)
- IRISSSM closed-loop control (CLC) technology
In order to better serve you, Sciaky offers financing and leasing options for U.S. customers who purchase EBAM™ systems, making it easier than ever to acquire this game-changing technology. Ask your Sciaky sales representative for details.
From EBAM® System Implementation & Training to Ongoing Support & Maintenance, Sciaky Is With You Every Step of the Way
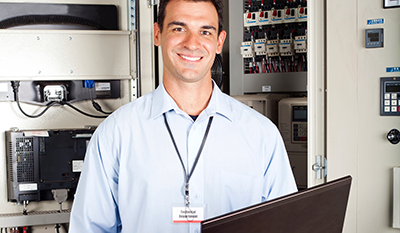
Sciaky’s metal 3D printing machine comes fully-loaded with state-of-the-art Electron Beam Additive Manufacturing (EBAM®) features and functionality from day one. Our turnkey package includes the installation of the EBAM system, all configuration and design software, and comprehensive training on all aspects of EBAM technology. We also provide remote production monitoring and on-site preventive and predictive maintenance agreements.
In most cases, our EBAM customers choose to develop procedures, prototypes and first-offs at our Chicago facility. We work together to transition the technology to your company and facility, which can include:
- Training on the engineering-related EBAM methods of CAD model design.
- Training on the CAD/CAM conversion of the deposition strategy through machine tool path generation.
- Training on machine operation and maintenance.
- Assistance with deposition of first article parts, and sometimes low-rate production, either on-site at Sciaky, or at the customer’s facility.
Contact us for more information about Sciaky’s additive manufacturing customer training, service and support packages.