An Inside Look at Titanium 3D Printing: Industries and Emerging Applications
Following the meteoric rise of 3D printed plastics over the last couple of decades, many manufacturing industries are quickly adopting 3D metal printing technology, especially for titanium alloys. Essentially, the process combines the material advantages of titanium with the unparalleled flexibility in product design and fabrication that you get with additive manufacturing.
Exploring New Product Possibilities with Additive Manufacturing
Traditionally, titanium was relatively challenging for manufacturers to work with. The metal’s chemical reactivity at high temperatures, low heat conductivity, and high hardness make it difficult (or prohibitively expensive) to machine or otherwise form into complex shapes. However, wielding new advances in titanium 3D printing technology, today’s manufacturers now have a better method for building high-precision titanium parts from scratch, one layer at a time.
Established and Emerging Applications for Titanium 3D Printing Technology:
Precision Aerospace Parts and Components
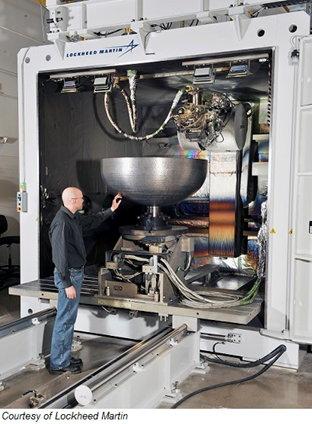
Aerospace parts typically are required to be exceptionally strong, lightweight, thermally stable, and highly resistant to corrosion. Titanium is therefore an ideal aerospace material. However, utilizing conventional CNC machining and other traditional manufacturing methods, aerospace manufacturers often face exceptionally high production costs and extended lead time.
For these reasons, the aerospace sector increasingly turns to titanium 3D printing as a better process for prototyping and for building certain specialized production parts. Additive manufacturing gives manufacturers much more flexibility in design for achieving high-precision part features and geometrical complexity. Some of the common applications include:
- Aerospace structural parts
- Airframe components
- High-performance aerospace fasteners and hardware
- Jet and propulsion system parts
- Turbine blades, shafts, housings, and related components
See our Lockheed Martin Space Systems case study for a look at aerospace titanium 3D printing in action
Defense Industry Equipment and Military Manufacturing
Similar to aerospace, the defense sector increasingly turns to titanium 3D printing for advanced prototyping, as well as for producing highly specialized components typically in low volumes. Military equipment is constantly evolving, helping to keep the American defense industry on the cutting edge of performance and capability.
With 3D titanium printing services, defense contractors now have a better way to develop new complex prototypes, to further optimize existing products, or to produce unique parts with quick turnaround and lower cost results. Common 3D printed titanium military equipment includes:
- Rocket propulsion
- Ground vehicle components
- High-performance structures and hardware
- Satellite and communications equipment
- Weapons mounts and turrets
- Wearable armor and field equipment (e.g. exoskeletons and joint reinforcements)
Industrial Equipment and the Manufacturing Sector
The modern industrial manufacturing sector is likewise no stranger to 3D metal printing. Just as with critical aerospace parts and military equipment, industrial manufacturers today often need advanced methods for rapid prototyping and product development.
In other cases, it may be the quickest and/or most cost-effective way to produce specialized industrial parts which are otherwise unavailable on the market – e.g. legacy parts, discontinued equipment, or replacement parts not available from the OEM. Typical uses for 3D titanium printing for industrial parts includes:
- Custom tooling solutions
- Transmission components
- Jigs, fixtures, and workholding devices
- Corrosion resistant valves, mixers, and impellers
- Specialized fasteners and hardware
Innovation in Additive Manufacturing for Tomorrow’s Aerospace Industry
Founded in 1939, Sciaky is backed by more than eight decades of innovation and manufacturing excellence in the cutting-edge aerospace industry and beyond. We’ve continuously embraced the rise of 3D metal printing across industries through the refinement of our innovative Electron Beam Additive Manufacturing (EBAM) processes.