Sciaky wins TCT Aerospace Application Award for EBAM® Metal 3D Printing Technology
The award acknowledges the significant time and cost savings achieved by Lockheed Martin Space Systems using Sciaky’s industry-leading EBAM metal additive manufacturing system
CHICAGO, Illinois | October 10, 2017
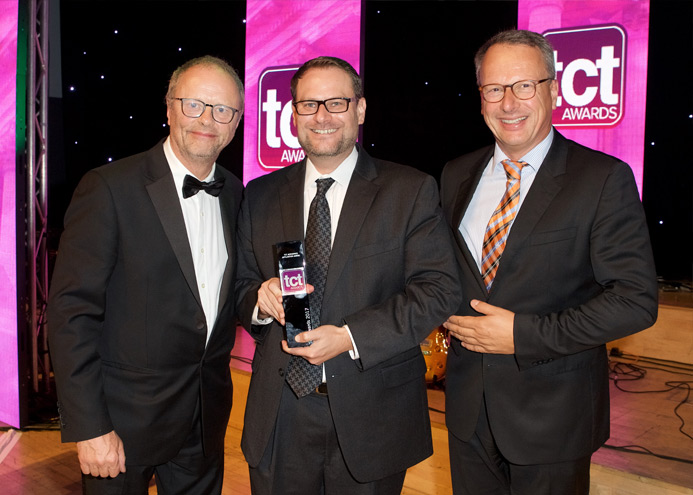
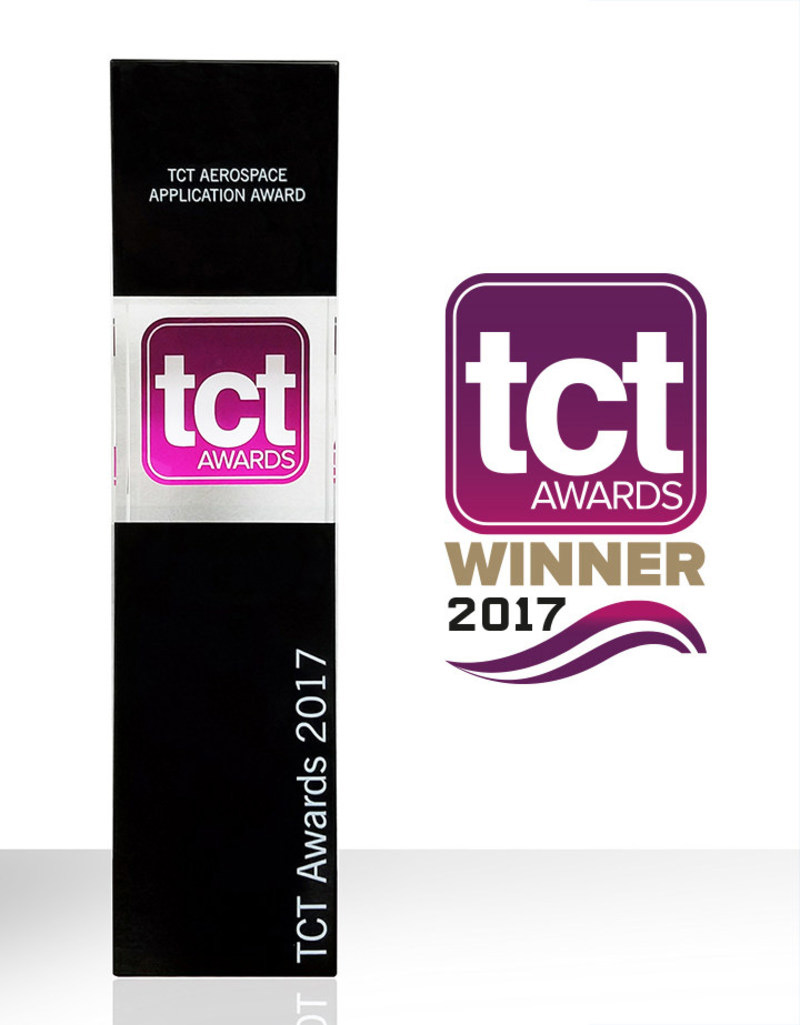
Sciaky, Inc., a subsidiary of Phillips Service Industries, Inc. (PSI) and leading provider of metal additive manufacturing (AM) solutions, announced today that it won the TCT Aerospace Application Award, along with Lockheed Martin, for the successful production of titanium propellant tanks using Sciaky’s industry-leading Electron Beam Additive Manufacturing (EBAM®) technology.
The TCT Awards, celebrating the innovators, technology and collaborators behind the best examples of 3D technology use across the globe, took place on September 26, 2017 at the Birmingham Town Hall in Birmingham, UK.
For this particular application, Lockheed Martin Space Systems reduced costs by 55%, material waste by 75%, and production time by 80% by using Sciaky’s EBAM metal 3D printing solution over traditional forging methods.
"Sciaky is honored to receive this prestigious award from the 3D printing experts at TCT, and in conjunction with the visionaries at Lockheed Martin Space Systems,” said Bob Phillips, Vice President of Sciaky, Inc. “This was truly a groundbreaking metal 3D printing application for the aerospace industry that highlighted the tremendous possibilities of additive manufacturing."
As the most widely scalable, metal additive manufacturing solution in the industry (in terms of work envelope), Sciaky’s EBAM systems can produce parts ranging from 8 inches (203 mm) to 19 feet (5.79 meters) in length. EBAM is also the fastest deposition process in the metal additive manufacturing market, with gross deposition rates ranging from seven to 20 lbs. (3.18 to 9.07 kg) of metal per hour. EBAM brings quality and control together with IRISS® – the Interlayer Real-time Imaging and Sensing System, which is the only real-time monitoring and control system in the metal 3D printing market that can sense and digitally self-adjust metal deposition with precision and repeatability. This innovative closed-loop control is the primary reason that Sciaky’s EBAM 3D printing process delivers consistent part geometry, mechanical properties, microstructure, and metal chemistry, from the first part to the last.
For more information on Sciaky, visit www.sciaky.com. You can also follow Sciaky on Twitter, Facebook, Google+, YouTube and LinkedIn.